Powder coating for aluminum and zinc die casting products
Powder coating for aluminum and zinc high pressure die casting products can effect both surface decoration and protection purposes. It is popular for die cast home appliance, telecommunication parts and display products. All these die cast products requires decoration surface neat and good looking. Powder coating can be well controlled in house so as to reduce environment impact, which is considered much more serious in China.
Parison die casting foundry has established long relationship with two powder coating factories through mutual benefit cooperation. Most powder coated parts of our die cast products are die cast lighting parts, telecommunication parts and photography appliance. As for some high requirement for salt spray testing, we apply world wide used powders like Akso, dupont for such die cast products.
Types of powder coating for die cast parts
1.Thermoplastic powder coating is one that melts and flows when heat is applied, but continues to have the same chemical composition once it cools and solidifies.
2.Thermosetting powder coatings also melt when exposed to heat. After they flow into a uniform thin layer, however, they chemically cross-link within themselves or with other reactive components. The final coating has a different chemical structure than the basic resin, is heat stable and, unlike thermoplastic powder after curing, will not soften back to the liquid phase when re-heated.
Process of powder coating for die cast parts
Powder coating is a dry finishing process, using finely ground particles of pigment and resin, which are electrostatically charged and sprayed onto electrically grounded aluminum casting parts. The charged powder particles adhere to the aluminum casting parts and are held there until melted and fused into a uniformally flowing coating in a curing oven.
Pretreatment of powder coating for die cast parts
aluminum casting parts to be powder coated first are exposed to a pretreatment operation to ensure that the surface to be coated is clean and free of grease, dust, oils, rust and other residue. The pretreatment process is normally conducted in dip tanks. Powder coating lines usually incorporate a chrome phosphate application step for aluminum casting parts that adds corrosion protection and improves the adhesion of the coating. After the aluminum casting parts have passed through all of the pretreatment steps, they are normally dried in a low-temperature dry-off oven. After drying, the aluminum casting parts are ready to be powder coated.
Come to other post treatment for die casting
- rapid prototype,die casting and mold design
- CNC machining, precision machining, finishing
- polishing,mirror polishing,brushing
- electroplating: nickel, chrome plating
- powder coating
- e-coating,electrodeposite,electrophoresis
- painting,lacquering,stoving varnish
- chromate passivation, phosphating
- impregnation
- laser cutting, silk screen
- sand blasting, ultrasonic cleaning, tumbling
- assembly and retail packaging
Powder coating of die casting products show
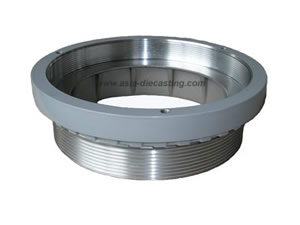
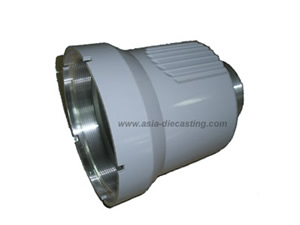
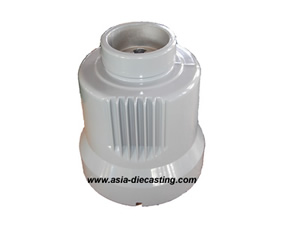