Painting, stoving varnish, lacquering for aluminum and zinc die casting parts
Painting for aluminum and zinc die casting products is a very common surface treatment offered by parison die casting. Painting can be divided into wet painting, stoving varnish, and lacquering. Wet painting is the cheapest and simplest, while stoving varnish is the most expensive and finest painting process. Lacquering is used for mirror polished or electroplated die cast products for surface protect.
Parison is experienced in handling painting for aluminum and zinc die casting products. We have several liable painting partners who can handling wet painting, stoving varnish and lacquering in house, and except extreme large parts, all of work pieces are processed by automatic lines. They have been offering service for famous companies like Philips, Motorola. The painted final products can be inspected by salt spray and scratch testing.
Wet painting for die casting products
Wet painting is to paint work pieces in color and let it dry in windy atmosphere without baking or any other drying by people, as features its process name. It is the cheapest and simplest painting means among these three painting processes, but with highest environment impact. If possible, please don't choose this process.
Wet painting is used for low class die casting products for slight surface protection. However some aluminum die cast electronic bike wheel hubs are wet painted in gray for surface decoration and protection. Such die cast wheel hub will be subject to dirty road environment, so costly decoration is wasting and not necessary. Generally speaking, some non-decoration die cast parts are suitable for wet painting as economical purpose.
Stoving varnish for die casting products
Stoving varnish is the most applied painting process here. Die cast work pieces are painted in dust-free house with automotive painting guns, then transported into baking house to make it adhered on the surface of die cast parts. In dust-free house, waste paint can be recycled for next time painting, and all the environment impact can be kept in control well. Furthermore, the baking step can speed up the whole painting process much quicker than wet painting process.
Most aluminum and zinc die cast lighting parts are processed by stoving varnish for surface decoration and protection. Besides, parison die casting has lots of furniture, die cast home appliance and display appliance are always required for stoving varnish treatment.
Come to other post treatment for die casting
- rapid prototype,die casting and mold design
- CNC machining, precision machining, finishing
- polishing,mirror polishing,brushing
- electroplating: nickel, chrome plating
- powder coating
- e-coating,electrodeposite,electrophoresis
- painting,lacquering,stoving varnish
- chromate passivation, phosphating
- impregnation
- laser cutting, silk screen
- sand blasting, ultrasonic cleaning, tumbling
- assembly and retail packaging
Lacquering for die casting products
Lacquering here is only referred to a protective painting means for mirror polished or electroplated die cast products using transparent paint. Mirror polished die cast parts can be subject to scratch, after lacquering the surface can be protected effective from scratch. As for electroplated parts, no matter chrome plated or nickel plated die casting surface are easy to react with oxygen in atmosphere, then with the protection of transparent lacquer, the surface can be free from reaction and keep vivid nature color of plating.
Painting of die casting products show
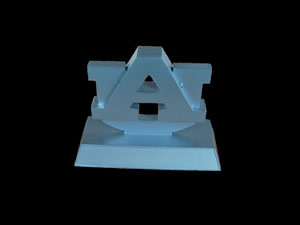
stoving varnish of die casting products
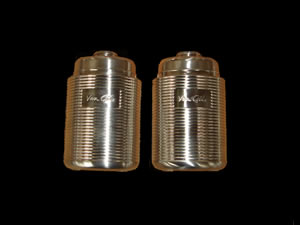