Aluminum extrusion parts converting to aluminum die casting parts
Aluminum extruded parts always require a uniform sectional view and without any draft angle. It is the very technique limitation that leads the engineering designer to choose other production process such as high pressure die casting. When the extrusion parts converted into die castings, the engineering designer can be released from its unique limitation, and add other features which are not the same through sectional view.
However,while being converted to high pressure die cast parts, other process limitation occurs. The initial limitation is the wall thickness should be increased at least up to 1.5-2 mm. As for aluminum extrusion parts, the wall thickness can be 0.5-1mm,which can't be obtained by high pressure die casting generally. Besides, draft angles and edge rounds should be added to the converting parts.
Aluminum extrusion technique database
Surface treatment: aluminum extrusion parts can be color anodized for its low silicon content. Besides it can be suited for other surface treatment like powder coating, electroplating, painting, electrophoresis, and polishing etc.
Heat treatment: aluminum extrusion parts can also be processed by heat treatment to improve its inner crystal and surface hardness.
Wrought alloy: aluminum extrusion uses wrought aluminum alloy which is not suited to casting, but has better plasticity.
Consistent sectional view: aluminum extrusion requires the same section through the whole part as per its process characteristic.
Notes of converting to die casting part
Reduction of mechanical property: the extruded parts have better toughness and hardness than die casting parts. Because we have to use die casting alloy instead of former wrought alloy and the die casting has its critical porosity in nature, such reduction of mechanical property can not be avoided. Furthermore, die castings are not suited to any kinds of heat treatment. We can't improve its inner structure any more except by impregnation.
Limitation of surface treatment: die castings can't be color anodized, which is only suited to black hard anodizing. Besides, because of porosity, die cast parts are hard to mirror polish, except that we use larger tonnage machining to cast otherwise it has to lead to high rejection rate.
Necessary design adaptation: the former extrusion parts should be increased the wall thickness, and added with draft angles to the involving plane and edge rounds, so as to be a ready and proper die casting
Come to other die casting conversions
Accepting die casting conversion projects
During the last three years,Parison has established two manufacturing factories in the mainland and been expanding our manufacturing capability in non-ferrous metal industry. In the near future, we are to set up aluminum extrusion and cold forging factories in Yangtze River district.
Our professional engineers team engaged in non-ferrous metal manufacturing are ready to assist you in product design, choosing production process and other engineering issues.
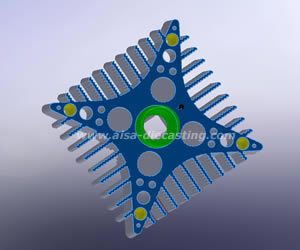
Moving die half of die cast parts converted from extrusion part
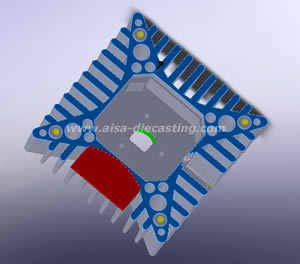